We provide training for industrial, commercial, healthcare, and property management maintenance folks. Our classroom has a limited number of seats as we keep our classes small so there's ample time for the instructor to spend with each student especially during the hands-on activities.
Facility Features
- Well equipped classroom
- Full size hands on training modules – training modules that can be powered up for real time learning
- ANSI pumps & NEMA motors on baseplates,
- split case pumps
- fractional up to multiple horsepower motors
- full size motor starters and modular test stands for electrical trainingtraining
Featured on 6 ABC (WPVI) in Philadelphia
Watch the video
Our Principal Trainers
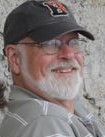
- Current: Owner – Maintenance Troubleshooting International LLC, 2917 Cheshire Road, Wilmington, DE 19810 (Successor to Maintenance Troubleshooting which was established in 1976) Advises & instructs on maintenance management programs, predictive/preventive maintenance programs, total productive maintenance, maintenance & production collaboration, storerooms and other associated maintenance related functions.
- Prior:Technical Manager for Rath USA, an international specialty refractories manufacturer. Built and operated a grass-roots facility for a foreign manufacturer in the USA. Set up preventive and predictive maintenance standards for machinery supplied from numerous countries.
- Operations & Logistics consultant for Endless Pools, Inc—manufacturer of induced current swimming pools. Troubleshot pump problems for sales personnel.
- Group Maintenance & Project Manager for Mannington Mills—commercial flooring manufacturer. Involved with packaging and web control machinery repair.
- Plant Superintendent for David J. Joseph Co—an international scrap processor.
- Facility Manager for the Delaware Reclamation Project—a world renowned municipal solid waste resource recovery facility.
- Maintenance & Utilities Manager for the A. E. Staley Manufacturing Company — a corn wet milling facility that included production of food grade products. Developed a unique in-house pump rebuilding program that is still used by Staley in all their plants today.
- Project engineer, Plant Engineer & Production Superintendent for Air Products &Chemicals.
- Project Engineer for Rohm & Haas Company
-
Current: Senior Electrical Instructor with Maintenance Troubleshooting, 1 ArlingtonStreet, Newark, DE 19711 (Established 1976) Writes electrical training programs, assists clients in setting up electrical PM programs. Qualified to train on Basic Industrial Electricity for the Multi-Craftsman, Industrial Electrical Troubleshooting, Advanced Industrial Electrical Troubleshooting, Electric Motor Control Circuits, as well a custom training on specific electrical components (control relays, molded case circuit breakers, fuses and disconnects, arc-flash safety requirements, capacitor installation on electric motors).
-
Prior: Owner of RHH Consulting- NEC and Electrical Safety Training– Instrument and Electrical Staff Manager with Formosa Plastics PVC Processing Plant, Delaware City, DE responsible for electrical and instrument selection, maintenance, repair, staffing, and training plant wide– Senior Electrical Supervisor—Electrical and Instrument Crafts with Stauffer Chemical, Headquarters in Westport, CT-hired and trained plant staff for grass roots plant and continued as supervisor of the electrical department
Randy Craps is a solid addition to Maintenance Troubleshooting International’s (MTI) list of subject matter experts with a dynamite field engineering background. Randy puts a southern drawl on his live training since he hails from and still resides in the State of Georgia. What you learn from being around Randy comes from his over 40 years of solid down-to-earth experiences. MTI uses training equipment developed by Randy for our well attended classes on variable frequency drives, introduction to programmable logic controllers and electric motor controls. (VFD-302, PLC-302, and EMC-302).
Education & Business:
Randy holds a degree from Midlands Technical College and a Master Electrical License in both South Carolina and his own state of Georgia. While employed at Southwire Corporation he earned the title of senior electrician, developed testing methods to troubleshoot complex control equipment and also trained the other electricians on those methods. Just before the plant closed the received his master electrician license and was invited by his instructors to come back to the Midlands Technical College to teach the night program. His field experience and knowledge of codes and electrical theory has been a valuable asset for teaching others. Randy has the ability to translate technical terminology effectively to students. For the past 8 years Randy has been operating his own training business where he makes use of the training equipment he builds for classes. When you attend a course where Randy is the trainer, you will find a fellow more than willing to explain complicated things twice because he wants you to know the subject as well as he does. Randy believes strongly if you want hands-on learning, that you need a “hands-on” guy teaching you.
Outside Interests:
Randy enjoys hobbies that relate to his profession. He builds and sells table top training equipment and simulators to colleges and high schools that stress the practical end of electricity. His equipment allows introduction of tricky troubleshooting problems that make a student think and solve problems in a non-threatening classroom environment allowing them to gain ground when a real situation presents itself back at their plant or facility.
Roger Wood is a mechanical maintenance engineer with over 30 years experience in a large paper mill located in Maine. His in-depth knowledge of troubleshooting and maintenance procedures on rotating equipment used in industrial applications such as pumps and mechanical drives is nothing short of amazing. Roger has extensive experience with preventive (PM) and predictive maintenance (PdM), best practices including lubrication, precision machinery alignment, and vibration analysis.
One of Roger’s troubleshooting stories that we found really interesting was an incident where the vibration analysis mechanic related an issue that just stumped him. He was trying to determine what was going on with an outboard anti-friction ball bearing on a 1000 HP fan pump supplying the head box on a large paper machine where successive vibration readings just didn’t make sense. Readings had been taken on a routine schedule, but the most recent reading dropped to an extremely low level from before. This pump was packed with braided packing inboard of the bearing. After hearing the mechanic’s explanation of what was going on, Roger suggested it was possible that bearing cage had broken, the balls had dropped out of the races and the packing was acting as a plain bearing. During inspection on the next scheduled outage, it was discovered that in fact the balls were missing and the packing had been carrying the load!! Yes, that was 1000 HP.
During his career, Roger has developed numerous maintenance training programs. His experience also includes work as a technical writer developing system description manuals used for training of operators and maintenance persons in the pulp & paper and oil and gas industry. He has a Mechanical Engineering degree from the University of Maine and has attended classes and seminars on fluid power, bearing failure analysis, lubrication, and vibration analysis. He is currently a key mechanical instructor with Maintenance Troubleshooting International, teaching classes at the company training facility and onsite at customer locations on centrifugal pump repair, maintenance and troubleshooting; troubleshooting rotating equipment as well as machinery alignment and hydraulics. Attendees at his classes remark about his depth of knowledge on machinery from his vast field experience. “My kind of engineer,” one mechanic had to say, “He understands field problems.”
Roger is a firm believer that knowledge is POWER. The more training and experience a maintenance person acquires the more value you provide your employer. The result is improved equipment uptime, higher company profitability and improved job security. Classes taught by Roger are both interesting and enlightening.
Bassem is a among the elite when it comes to solving mechanical problems. He is a mechanical engineer and has worked for some of the best – John Crane as a Field Engineer for 5 years, Eaton Aerospace as an R & D Engineer for 4 years, Kingsbury Bearings as a Design Engineer for 3 years & currently for Flowserve, the worlds largest manufacturer of pumps in various engineering roles for 14 years. He has a special focus at Flowserve on Mixers & Specialty Equipment. Flowserve has generously agreed to allow Bassem to use his vast experience so that MTI can continue to bring the best Hands-on instructors to our Hands-on Training Center.
What makes Bassem an interesting fellow to listen to & learn from? How about the fact that he came up with a successful solution to seal latex at a major Dow Chemical plant in the Netherlands – so impressive that he was awarded the First Flowserve Seal Division Achievement Award. If that isn’t enough then how about this – He led a team of Flowserve engineers to work on sealing a Tyvek application at 4000 P, 550F with a gearbox built into the seal – a first. This had to be accomplished using a dual seal design where the outboard too k the brunt of the 4000 psi. It was installed in March 2021 at a DuPont Tyvek facility in Virginia and is performing better than expected.
So, if you think one of your seal or pump problems can’t be solved, you haven’t met Bassem!!
Ed has an engineering degree from Drexel University, but more importantly values his experiences solving rotating equipment problems. He is a certified Maintenance & Reliability Professional who gets knee deep in his challenges. Ed has worked as an Application Engineer as well as a Regional Reliability Engineer at Flowserve. He served as a site Rotating Equipment Specialist at Exelon followed by a Corporate Rotating equipment Engineer role at DuPont. After a four year stint away from Flowserve, he returned to them to serve as the North American Alliance Manager and has served in an engineering manager capacity for the past five years. If Ed hasn’t seen it all, he’s certainly seen a lot of it!
In his spare time, Ed likes to use his mechanical ingenuity & curiosity to explore & put into practice things the rest of us only think about. He actually converted his VW TDI Diesel to run on 100% homemade bio-diesel made from restaurant’s waste vegetable oil. Lastly if you look closely at Ed’s picture, you can see that he is a passionate Philadelphia Eagles fan. So even if you are not an Eagles fan, Ed will still like to talk football!
Stan is a Mechanical Engineer with a penchant for understanding the intricacies of rotating equipment. He has over 30 years of Rotating Machinery & Reliability analysis experience in power generation, petrochemical, pulp/paper, and wastewater facilities. Prior to founding M&B Engineered Solutions in 2005, he managed and staffed GE / Bently Nevada’s Machinery Diagnostic Services (MDS) and Asset Care teams for almost 20 years. He specializes in critical rotating machinery analysis & inspection, balancing of large turbo-machinery trains, modal & ODS analysis, optical & laser alignment and predictive maintenance. Equipment that Stan has worked on to successfully address problems include – compressors, boilers and process fans, cooling tower fans, vertical and horizontal pumps, reciprocating engines, gearboxes, steam turbines up to 1200 MW, gas turbines and many more, too numerous to mention.
Being an ISO-Certified Vibration Analyst, Category IV, he has authored & presented technical papers covering diagnostic techniques, balancing, modal analysis, optical alignment, condition monitoring systems integration, and lube oil analysis. He earned a Bachelor of Science degree in Mechanical Engineering from Penn State University in 1985, and a Masters Degree in Business Administration (Finance) from Wilkes University in 2009. He is a registered Professional Engineer in the commonwealth of Pennsylvania. With earlier Six Sigma Green Belt certification, he continues to focus on customer-based reliability improvement projects. He is also a member of the American Society of Mechanical Engineers and is a Certified Maintenance & Reliability Professional (CMRP) through the Society for Maintenance & Reliability Professionals.
In his spare time, Stan enjoys spending time with family & friends, boating, hunting, fishing & cycling.
Joe is a highly skilled safety, health and environmental (SHE) professional who puts a practical spin on working safely. With over 50 years of experience, he continues to provide targeted training in safety and health and maintenance-related procedures. He conducts workplace health and safety inspections; creates, updates or improves SHE programs and procedures to ensure they are the best in class. He currently serves on the local health professional board and on various military-support focused organizations. He has authored two chapters in professional reference books.
Joe earned a B.S. in Chemical Engineering from Drexel University and has extensive military experience, having served in the Army National Guard and Army Reserves for 25 years. He remains active in supporting those organizations by serving on the Executive Committee (and former Commander) of the Honorary First Defenders of Allentown, PA and serving as the East Central Area Chair of DOD’s Employer Support of the Guard and Reserve.
Joe has belonged to the Chemical Council of New Jersey Environmental and Health and Safety Committees as well as numerous organizations.
Throughout Joe’s career he has worked for Liberty Mutual Insurance Company, Air Products and Chemicals, Inc., ARCO Metals Corporation, AT&T Bell Labs, CasChem Chemical Company, Cosan Chemical Company, Hoffmann LaRoche, DSM Nutritional Products and Roux Associates, Inc in various capacities.
He has also provided SHE services for: ExxonMobil, Conoco/Phillips, Johnson and Johnson, Bosch Rexroth, Vornado, O’Neill, Pfizer, Blue Islands Phenol, Berks Packing Company, DF Stauffer Company, RHI Magnesita and numerous safety program reviews/inspections for companies required to reduce their workers compensation injury experience.
Joe is a published author having written “Alkyl Amines”, Chapter 6 in Industrial Hygiene Aspects of Plant Operations, Volume I, Process Flows, MacMillan Publishing Company, Inc. as well as “Alkyl Amines”, Chapter 3 in In-Plant Practices for Job Related Health Hazards Control, Volume I, Production Processes, John Wiley and Sons.
Joe has tackled some notable & unique projects during his career. He brought his practical knowledge to bear when asked to provide guidance to both the production & maintenance crews in a chemical plant where a mutagenic chemical had to be used to clean stubborn reactor fouling. Although the plant routinely handled flammable & explosive materials, this was a new wrinkle so all of the working parties were understandably nervous. Combining his chemical engineering and safety backgrounds, he was able to provide the guidance that allowed plant personnel to go about handling the material with confidence and without incident.
Joe’s passion is helping people remain safe while providing a better environment for the next generation. In his spare time he enjoys watching golf tournaments (he was an avid golfer as a junior), target shooting, dining out, traveling, and spending time with his grandchildren.
If you want a practical take on Maintenance Safety from one of the best and most relatable safety professionals around, then you want to attend one of Joe’s classes. [Note from the MTI management – we actively searched Joe out (& only Joe) as the instructor for this course.]
Bill Anthes is a fellow that has a penchant for learning while having tons of boots on the ground experience. His educational credits include stints at Forest Park Community & Vatterott Colleges in St. Louis, Missouri as well as Delaware Technical Community College in Newark, Delaware.
Bill has worked as Journeyman mechanic with experience in various industries as well as a Pipefitter, Millwright and Crew Leader. His industrial experience includes automotive, steel, refineries, power stations, pulp/paper & chemicals. He has maintenance experience with boilers, instrumentation, control systems, fire protection systems, pneumatics & hydraulics. He also has some very specialized experience with equipment in the aerospace & defense industries. It’s a rare occasion that you can stump Bill with something he hasn’t seen during his career.
In addition to the areas of expertise already mentioned, Bill has developed proficiency in HVAC, predictive & preventive maintenance and utilities. In other words, Bill has a really broad background and is excited to pass along the knowledge he has amassed over the years. His natural demeanor lends itself to an informative & fun learning experience. You’ll want to include some of Bill’s classes on your list of classes to take.
Andy is a Mechanical / Structural Engineer with BS and MSME degrees from Widener University. He was raised on a dairy farm and like most farmers learned early on how to be creative to fix and improve things. He is a registered Professional Engineer in Delaware, New Jersey and Pennsylvania. as well as a Professional Planner and Certified Municipal Engineer in New Jersey. He has over 35 years of diverse technical experience and project management leadership in the mechanical, chemical, civil, and environmental engineering disciplines in Plant Engineering, Facilities Management and Municipal Engineering. The bulk of his experience has been in heavy industrial applications including Ship Building, Steel Mills, Alloy and Metals Plants and VCT Flooring Manufacturing. Andy has been involved with all stages of plant improvement projects from initial evaluation, engineering design and equipment selection, installation, start up, maintenance and retrofits. Some of the various equipment and systems that Andy has developed a level of expertise working with include: size reduction, pneumatic conveying, pump transfer stations, material handling, batching scale systems, blenders, dust collection systems, sheet calendaring systems, heat exchangers and cooling systems, packaging systems, furnace operations (arc, gas & induction), clarification and water treatment systems. Andy established a maintenance system in a start-up operation containing a PM program which included lubrication analysis, vibration analysis and infrared scanning. Andy has also developed a functional storeroom operation for spare parts and consumables for an entire plant. He has been part of a new business development team evaluating capital costs and operational processes of companies considered for acquisition. Andy has also served as Chairman for Investigation Improvement Safety Committee for an entire plant.
Andy is regarded as a problem solver who will do whatever it takes to get the job done. He recently was the project manager for Clyde Bergemann Power Group (CBPG) and responsible for the installation of the first dry bottom ash handling system in the US at Seminole Electric in Palatka, FL. These systems were installed on two 800 MW boiler units. Following that project Andy was responsible for the installation of Submerged Scraper Conveyors (SSC) and auxiliary conveying systems on four 700 MW units and two Remote Submerged Scraper Conveyors (RSSC) at Santee Cooper in Pineville, SC. While working for CPBG, Andy was responsible for all Field Service and system start-ups which included training the maintenance and production staffs of the facilities in the operation and maintenance of pneumatic and mechanical conveying systems, dry sorbent inject systems and dust collection systems. Through his career Andy has had numerous training opportunities in Project Management, Reliability Engineering, Root Cause Analysis and PLC Courses. Andy has always enjoyed training opportunities and interfacing with maintenance personnel. Over the years he has learned as much or more from them than his professors in college (and he had some pretty good professors in college) because he was never afraid to get his hands dirty & dive into the problem right along with them!
Andy is a passionate Philadelphia sports fan who has lived through “trusting the process” with the 76ers. He enjoys sporting events with his sons and friends, concerts and traveling with his wife. He relaxes by working out and riding his motorcycle and is an avid reader.
- Owner of Industrial Trainers of America – Business started in 1997.
- Universal Refrigeration Certification
- Vetted Proctor for EPA Test for Certified Refrigeration Technician
- Technical Course Design and Author
- Pumps and Pumping Systems – ITA Technical Publishing Institute.
- Used in municipal water and waste treatment plants in over 50 USA cities
- Chosen as the training syllabus on pumps for MTI Training Center
- Bearing Technology and Failure Analysis – ITA Technical Publishing Institute
- A unique and well illustrated guide to allow maintenance mechanics to under stand how to install and prolong the life of anti-friction bearings.
- Precision Measurement – Tolerances for rebuilding of mechanical equipment
- Fans and Blowers – Classroom book for HVAC and Building Technicians
- Industrial Electricity – Award winning text book & tabletop test board combination
- Audel Mechanical Trades Pocket Manual – Published by John Wiley & Sons, Inc. covers machinery installation, bearing installation, gears & gearing, shafting, bearings and measurements as well as a myriad of other useful subjects. Over 750,000 copies in print.
- Audel Millwright and Mechanics Guide – Published by John Wiley & Sons, Inc. covers detailed installation and rebuilding of complex equipment, bearing failure & correction, vibration analysis techniques for machinery inspection and repair standards. Over 1500 pages with field illustrations.
- Plant Services Magazine – Predictive Maintenance Correction
- Del-Tech Publications – The Four Step Method of Coupling Alignment